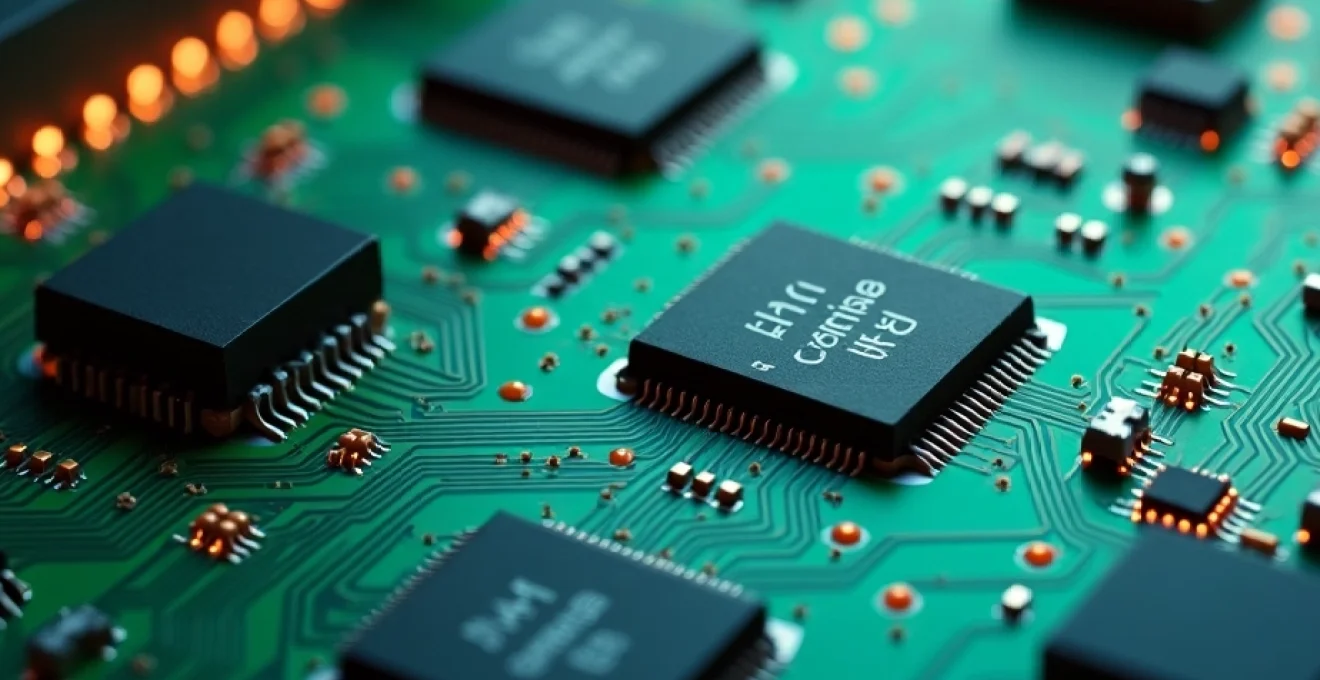
L'evoluzione dell'elettronica moderna è strettamente legata ai progressi nella tecnologia dei circuiti stampati. In particolare, i circuiti stampati ad alta densità di interconnessione (HDI) rappresentano oggi una soluzione fondamentale per realizzare dispositivi sempre più compatti, potenti e funzionali. Questa tecnologia avanzata consente di aumentare drasticamente la densità dei componenti e delle connessioni su un singolo substrato, aprendo nuove possibilità di miniaturizzazione e integrazione. Scopriamo insieme le caratteristiche principali, i processi produttivi e le applicazioni più innovative dei circuiti HDI, una tecnologia destinata a plasmare il futuro dell'elettronica.
Fondamenti della tecnologia HDI per circuiti stampati
I circuiti stampati HDI (High Density Interconnect) rappresentano l'evoluzione dei tradizionali PCB, consentendo di realizzare interconnessioni ad altissima densità. La caratteristica principale di questa tecnologia è l'utilizzo di microvie , ovvero fori di dimensioni molto ridotte (tipicamente inferiori a 150 μm di diametro) che permettono di creare connessioni tra i vari strati del circuito. Questo approccio consente di aumentare drasticamente il numero di connessioni per unità di superficie, arrivando a densità fino a 10 volte superiori rispetto ai PCB convenzionali.
Un altro elemento distintivo dei circuiti HDI è l'impiego di tracce e spazi tra le piste estremamente sottili, con larghezze che possono scendere fino a 50 μm o meno. Questa miniaturizzazione delle interconnessioni permette di realizzare layout molto più compatti, ideali per dispositivi elettronici moderni che richiedono elevate prestazioni in spazi sempre più ridotti.
La struttura tipica di un circuito HDI prevede l'utilizzo di tecniche come il build-up sequenziale , che consente di aggiungere strati sottili uno alla volta partendo da un nucleo centrale. Questo approccio offre grande flessibilità nel design e permette di ottimizzare il routing delle interconnessioni. L'impiego di materiali dielettrici avanzati e di tecniche di laminazione precise garantisce inoltre eccellenti proprietà elettriche e meccaniche.
Materiali avanzati e processi di fabbricazione HDI
La realizzazione di circuiti stampati HDI richiede l'impiego di materiali avanzati e processi produttivi altamente sofisticati. Solo attraverso tecnologie all'avanguardia è infatti possibile ottenere le elevatissime densità di interconnessione che caratterizzano questi circuiti. Vediamo nel dettaglio i principali elementi che compongono la "ricetta" dei PCB HDI moderni.
Substrati in resina epossidica ad alta densità
Il materiale di base per i circuiti HDI è costituito da substrati in resina epossidica rinforzata con fibra di vetro, simili a quelli utilizzati nei PCB tradizionali ma con caratteristiche ottimizzate per le alte densità. Questi materiali presentano una maggiore stabilità dimensionale, fondamentale per mantenere l'allineamento delle microvie, e migliori proprietà dielettriche per garantire l'integrità dei segnali ad alta frequenza.
Vengono inoltre impiegati substrati ultrasottili, con spessori che possono scendere fino a 50 μm o meno per i layer più esterni. Questo permette di realizzare stack-up complessivi molto compatti, ideali per dispositivi miniaturizzati. L'impiego di resine con bassa costante dielettrica e basso fattore di dissipazione contribuisce inoltre a migliorare le prestazioni elettriche complessive del circuito.
Tecniche di microvia e via cieca
Le microvie rappresentano l'elemento chiave della tecnologia HDI. Questi fori di dimensioni ridottissime vengono realizzati tipicamente tramite foratura laser, che consente di ottenere diametri inferiori a 100 μm con estrema precisione. Le microvie possono essere di tipo "cieco" (blind via), collegando solo alcuni strati adiacenti, o "sepolto" (buried via), completamente inglobate all'interno del PCB.
Una tecnica avanzata è quella delle microvie "stacked" o impilate, dove più microvie vengono allineate verticalmente creando connessioni che attraversano più strati. Questo approccio consente di ottimizzare ulteriormente il routing e aumentare la densità di interconnessione. La metallizzazione delle microvie richiede processi specifici per garantire una perfetta conducibilità elettrica nonostante le dimensioni ridotte.
Processi di metallizzazione selettiva per HDI
La creazione delle piste conduttive nei circuiti HDI avviene tramite sofisticate tecniche di metallizzazione selettiva. Il processo più comune è quello additivo, dove il rame viene depositato solo nelle aree desiderate anziché essere rimosso da un layer continuo come nei PCB tradizionali. Questo approccio consente di ottenere tracce estremamente sottili e precise.
Vengono impiegati anche processi semi-additivi, che combinano la deposizione selettiva con una successiva fase di etching controllato. La placcatura del rame viene effettuata utilizzando bagni chimici o elettrochimici altamente performanti, in grado di depositare strati uniformi anche all'interno delle microvie. L'impiego di finiture superficiali come l'ENIG (Electroless Nickel Immersion Gold) garantisce un'eccellente saldabilità e protezione dall'ossidazione.
Fotolitografia ad alta precisione per tracce ultrafini
La creazione dei pattern delle piste conduttive nei circuiti HDI richiede tecniche fotolitografiche estremamente avanzate. Vengono utilizzati fotoresist ad alta risoluzione e sistemi di esposizione laser direct imaging (LDI) in grado di trasferire sul substrato i dettagli più fini del layout. Questo consente di realizzare tracce con larghezze inferiori a 50 μm e spazi tra le piste altrettanto ridotti.
Il processo fotolitografico deve essere controllato con estrema precisione per garantire la ripetibilità delle geometrie su larga scala. Vengono impiegate tecniche di compensazione ottica e correzione delle distorsioni per mantenere l'accuratezza dimensionale su tutta la superficie del pannello. Solo attraverso questi processi all'avanguardia è possibile ottenere le altissime densità di routing caratteristiche dei circuiti HDI.
La produzione di circuiti HDI richiede un connubio di materiali avanzati, processi di precisione e tecnologie innovative. Solo le aziende in grado di padroneggiare queste competenze possono realizzare PCB HDI di ultima generazione.
Come si può intuire, la realizzazione di circuiti HDI è un processo altamente complesso che richiede tecnologie e competenze specifiche. Non tutte le aziende sono in grado di gestire internamente l'intero ciclo produttivo, per questo molte realtà si affidano a partner specializzati come icape-group.com per la fornitura di PCB HDI di alta qualità. La scelta del fornitore giusto è fondamentale per garantire prestazioni e affidabilità ottimali.
Progettazione e layout di circuiti HDI
La progettazione di circuiti stampati HDI richiede competenze specifiche e l'utilizzo di strumenti software avanzati. Il layout di questi PCB ad altissima densità presenta infatti sfide uniche rispetto ai circuiti tradizionali. Vediamo i principali aspetti da considerare e le tecniche più efficaci per ottimizzare il design di circuiti HDI.
Software CAD specializzati per HDI (altium designer, cadence allegro)
Per gestire efficacemente la complessità dei circuiti HDI è fondamentale utilizzare software CAD specifici, in grado di supportare tutte le peculiarità di questa tecnologia. Tra i più diffusi troviamo Altium Designer
e Cadence Allegro
, che offrono funzionalità dedicate come:
- Gestione avanzata delle regole di design per microvie e stackup HDI
- Routing automatico ottimizzato per alte densità
- Simulazione elettrica e termica integrata
- Verifica DRC (Design Rule Check) specifica per HDI
- Generazione automatica di stackup HDI complessi
Questi strumenti consentono ai progettisti di sfruttare appieno le potenzialità della tecnologia HDI, automatizzando molti processi e riducendo il rischio di errori. La curva di apprendimento può essere ripida, ma padroneggiare questi software è essenziale per realizzare design HDI ottimali.
Tecniche di routing ad alta densità e fan-out
Il routing delle interconnessioni in un circuito HDI richiede tecniche specifiche per sfruttare al meglio lo spazio disponibile. Una strategia chiave è il fan-out , che consiste nel distribuire le connessioni dai componenti più densi (come BGA) verso l'esterno utilizzando microvie. Questo permette di "aprire" il routing e sfruttare più layer per le interconnessioni.
Altre tecniche importanti includono:
- Routing differenziale per segnali ad alta velocità
- Utilizzo di via-in-pad per ridurre l'ingombro
- Ottimizzazione della distribuzione di potenza e massa
- Routing a "serpentina" per equalizzare le lunghezze
L'obiettivo è massimizzare la densità di routing mantenendo al contempo l'integrità dei segnali. Questo richiede un'attenta pianificazione e l'utilizzo di strumenti di simulazione per verificare le prestazioni elettriche.
Gestione dell'impedenza controllata in HDI
Nei circuiti HDI, il controllo dell'impedenza delle interconnessioni è fondamentale per garantire l'integrità dei segnali ad alta velocità. La gestione dell'impedenza controllata richiede una precisa calibrazione dello stackup del PCB, considerando parametri come:
- Spessore e costante dielettrica dei materiali
- Larghezza e spessore delle tracce
- Distanza dai piani di riferimento
- Effetti di accoppiamento tra tracce adiacenti
I software CAD moderni offrono strumenti avanzati per calcolare e ottimizzare l'impedenza delle interconnessioni. È importante lavorare a stretto contatto con il produttore del PCB per garantire che i parametri di progetto vengano rispettati durante la fabbricazione.
Ottimizzazione termica nei design HDI
L'elevata densità di componenti e interconnessioni nei circuiti HDI può portare a sfide significative nella gestione termica. È fondamentale adottare strategie di design che favoriscano la dissipazione del calore, come:
- Utilizzo di piani termici dedicati
- Posizionamento strategico di via termiche
- Impiego di materiali ad alta conducibilità termica
- Simulazione termica per identificare hot-spot
Un'attenta progettazione termica è essenziale per garantire l'affidabilità a lungo termine del circuito, soprattutto in applicazioni che richiedono elevate prestazioni in spazi ridotti.
Applicazioni chiave dei circuiti HDI nell'elettronica moderna
I circuiti stampati HDI trovano oggi applicazione in numerosi settori dell'elettronica, dove le esigenze di miniaturizzazione e alte prestazioni sono particolarmente spinte. Vediamo alcuni degli ambiti in cui questa tecnologia sta giocando un ruolo chiave.
Smartphone e dispositivi mobili ultrasottili
Gli smartphone moderni rappresentano forse l'esempio più evidente dei vantaggi offerti dalla tecnologia HDI. La necessità di integrare un numero sempre maggiore di funzionalità in dispositivi sempre più sottili ha spinto i produttori ad adottare massicciamente i circuiti HDI. Questi consentono di realizzare PCB estremamente compatti, con un elevato numero di layer interconnessi tramite microvie.
L'impiego di circuiti HDI permette di ottimizzare il layout interno degli smartphone, lasciando più spazio per componenti critici come la batteria. La possibilità di realizzare tracce ultrasottili consente inoltre di gestire efficacemente i segnali ad alta frequenza necessari per le comunicazioni wireless di ultima generazione.
Sistemi avionici e aerospaziali miniaturizzati
Nel settore aerospaziale, dove peso e dimensioni sono parametri critici, i circuiti HDI stanno trovando sempre più applicazioni. La possibilità di concentrare un'elevata potenza di calcolo in PCB ultracompatti è fondamentale per sistemi avionici avanzati, satelliti e veicoli spaziali.
La tecnologia HDI consente di realizzare computer di bordo, sistemi di navigazione e apparati di comunic
azione avanzati. La capacità di resistere a condizioni ambientali estreme e la grande affidabilità dei circuiti HDI li rendono ideali per queste applicazioni mission-critical.
Dispositivi medici impiantabili ad alta integrazione
Il settore medicale sta beneficiando enormemente della miniaturizzazione resa possibile dai circuiti HDI. Dispositivi impiantabili come pacemaker, neurostimolatori e pompe per insulina richiedono PCB estremamente compatti ma al contempo affidabili e performanti. La tecnologia HDI consente di integrare un'elevata funzionalità in volumi molto ridotti, migliorando il comfort del paziente.
L'impiego di circuiti HDI permette inoltre di realizzare dispositivi medici indossabili sempre più sofisticati, in grado di monitorare parametri vitali in tempo reale e comunicare con smartphone o altri apparati. La possibilità di gestire segnali analogici e digitali ad alta velocità su PCB ultracompatti è fondamentale per queste applicazioni.
Computer portatili e tablet di nuova generazione
Nel settore dei computer portatili e dei tablet, la tecnologia HDI sta permettendo di realizzare dispositivi sempre più sottili e leggeri, senza compromessi sulle prestazioni. L'impiego di circuiti ad alta densità consente di ottimizzare il layout interno, lasciando più spazio per batterie di maggiore capacità o sistemi di raffreddamento più efficienti.
I PCB HDI sono fondamentali per gestire le interconnessioni ad alta velocità richieste dalle CPU e GPU di ultima generazione, garantendo al contempo un'eccellente integrità del segnale. La possibilità di realizzare design compatti facilita inoltre l'integrazione di funzionalità avanzate come schermi touch, sistemi audio di qualità e connettività wireless multi-standard.
Sfide e innovazioni future nella tecnologia HDI
Nonostante i notevoli progressi degli ultimi anni, la tecnologia HDI continua ad evolversi per soddisfare le crescenti esigenze dell'elettronica moderna. Vediamo alcune delle principali sfide e innovazioni che stanno plasmando il futuro di questa tecnologia.
Integrazione di componenti embedded in substrati HDI
Una delle frontiere più promettenti è l'integrazione di componenti attivi e passivi direttamente all'interno del substrato HDI. Questa tecnica, nota come "embedding", consente di ridurre ulteriormente le dimensioni complessive del PCB e migliorare le prestazioni elettriche. Resistenze, condensatori e persino chip integrati possono essere inglobati tra gli strati del circuito, ottimizzando il routing e riducendo le interferenze.
Le sfide principali riguardano la gestione termica dei componenti embedded e la loro testabilità. Sono in fase di sviluppo nuovi materiali e tecniche di produzione per superare questi ostacoli e rendere l'embedding una tecnologia matura per la produzione di massa.
Circuiti HDI flessibili e stretchable per wearable
Il crescente mercato dei dispositivi indossabili sta spingendo lo sviluppo di circuiti HDI flessibili e persino estensibili. Queste tecnologie consentono di realizzare PCB in grado di adattarsi a superfici curve o di resistere a deformazioni ripetute, ideali per smartwatch, abiti intelligenti e dispositivi medicali indossabili.
Le sfide includono lo sviluppo di materiali conduttivi flessibili con prestazioni paragonabili al rame, e di tecniche di interconnessione affidabili anche in condizioni di stress meccanico. Stanno emergendo soluzioni innovative come l'uso di nanoparticelle metalliche su substrati polimerici e tecniche di laminazione avanzate per circuiti multi-layer flessibili.
Tecnologie di packaging avanzate (SiP, PoP) con HDI
L'integrazione della tecnologia HDI con soluzioni di packaging avanzate come System-in-Package (SiP) e Package-on-Package (PoP) sta aprendo nuove possibilità di miniaturizzazione. Questi approcci consentono di combinare più die di silicio e componenti passivi in un unico package ultra-compatto, sfruttando le interconnessioni ad alta densità offerte dai substrati HDI.
Le sfide principali riguardano la gestione termica di questi package ad alta integrazione e la necessità di tecniche di test e ispezione sempre più sofisticate. Lo sviluppo di nuovi materiali termoconduttivi e l'impiego di tecnologie di imaging 3D stanno contribuendo a superare questi ostacoli.
Sostenibilità e riciclabilità dei circuiti HDI
Con la crescente attenzione alla sostenibilità ambientale, il settore dei PCB HDI sta affrontando la sfida di ridurre l'impatto ecologico di questi prodotti ad alta tecnologia. Sono in fase di sviluppo nuovi materiali biodegradabili per i substrati e tecniche di produzione a basso impatto ambientale.
Un'altra area di ricerca riguarda il miglioramento della riciclabilità dei circuiti HDI a fine vita. Le elevate densità di interconnessione e la presenza di materiali diversi rendono complesso il recupero delle materie prime. Nuovi approcci come il "design for disassembly" e tecniche di separazione avanzate stanno cercando di affrontare questa problematica.